Controlling Concrete Cracks
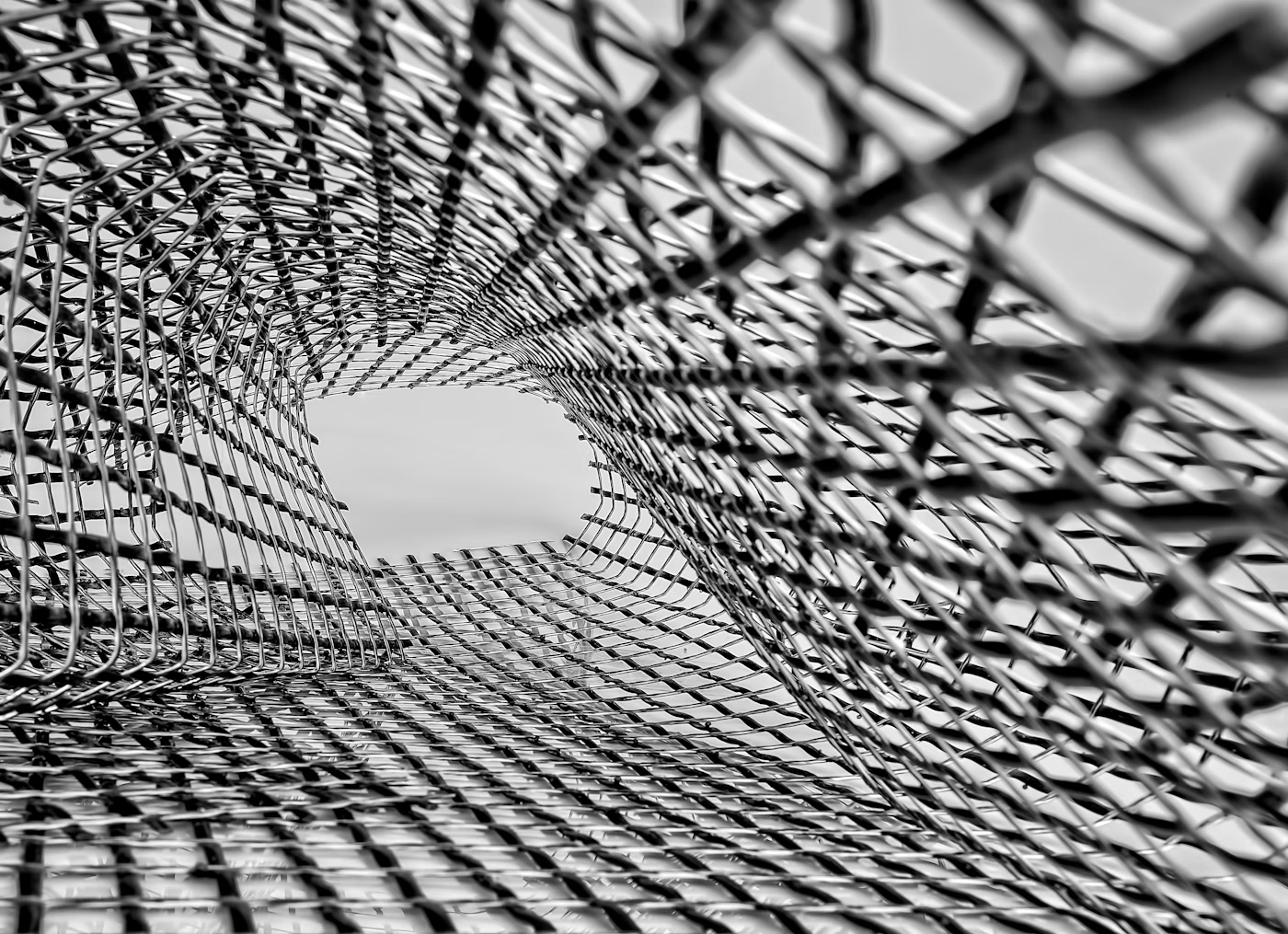
By its own nature, concrete is a brittle material. Its capabilities is performing well in compression but it is less effective when in tension. This is why, as had been discovered by a gardener, it needs reinforcement.
Technically, the Mesh Reinforcement in concrete is actually used to absorb the tensile forces so that the cracking which occurs in all high-strength concrete does not weaken the structure.
Strength improvement
A reinforcing ‘rebar’ mesh, or steel fabric, is a premade lattice of rebar used to improve the lateral strength of concrete slabs, walls, and other constructions. There are also standardized mesh fabric (such as A193, or B785) that refer to the cross-sectional areas of the mesh per square meters.
If you have one, your architect or structural engineer will tell you the type of mesh you need for your specific application.
Mesh
Reinforcement mesh is predominantly used as reinforcing fabric in concrete slabs. Being immersed in concrete, it vastly increases the structural rigidity of a construction.
Steel mesh fabric has a similar coefficient of thermal expansion to concrete, meaning that with temperature fluctuations, both concrete the steel embedded in it expand and contract at similar rates.
This makes it an ideal material to help reinforce concrete structures like pathways, driveways and garden groundwork.
Reinforcement
Steel, in the form of bars or mesh (popularly known as “rebar”) had long been in use as a reinforcement for concrete slabs that are designed to experience some form of loading.
The term “loading” means carrying traffic, spanning a void or bearing another structure such as a wall.Steel mesh has also been used as a raw method of crack control in the forces within the concrete.
As per the latest in concrete technology, there are now reinforcements in the form of fibres (polypropylene fibres) as well as glass or steel fibres. These reinforcements with fibresis predominantly used for preventing crack control in concrete structures rather than structural strengthening.
Steel
Where steel reinforcement of a slab is required for structural reasons, the specification will more than likely require high-tensile steel bars as well as fabric mesh. More important, the design should be done by a qualified engineer.
Steel mesh comes in a wide array profile with varying mesh sizes and wire sizes as indicated in the table opposite. Known as “fabric”, these steel mesh (4800mm X2400 mm) are cut to required size on site by means of a cut-off saw or ‘croppers’.
High-tensile steel bars are regularly used in ground beams and vertical structures. Bar steel is also commonly used in toed garage and house slabs or rafts where the building is to be constructed from brickwork.
Fibres
While steel reinforcement is still widely used for structural works, the development of fibre reinforcement over recent years has seen a shift away from the traditional steel mesh for crack control in plain slab work.
Special-use concretes may be reinforced with steel or glass fibres, but, the most commonly used fibre reinforcement is usually polypropylene or polyester.
Steel fibres are now popularly used on many of the large edge-of-town retail developments, commercial blocks and the distribution warehouses. They have their ground floor slabs (and mezzanine slabs) constructed using concrete containing steel fibres.
These are often added to the truck-mixer on site (by means of a conveyor or blasting machine) along with a generous addition of super-plasticizer to provide the workability needed to place it.
The addition of steel fibres makes the treated concrete quite expensive. However, compared to the cost of buying conventional steel mesh reinforcement and the associated storage, cutting, placing, etc., it usually works out to be quite competitively priced for the contractor and/or the client.
Fibres in concrete
Many of today’s high-quality batch-mixed concretes incorporate fibres of one type or another as their relatively low cost is more than justified by the benefits brought about by their inclusion.
Most ready-mixed concretes supplied for decorative concrete work rely on the fibre content to achieve the high-quality finish required for that type of prestige paving. The fibres work by “tying together” the concrete during placement, during and after curing has been completed.
Reduce segregation
In the placement, the fibres help reduce segregation of the fines and the cement immediately following placement, thereby ensuring a more competent concrete.
During curing, the fibres absorb most of the tensile forces caused by the natural shrinkage of the mix as it changes state from a freshly-placed liquid to a fully-cured solid.
The fibres must be properly and thoroughly dispersed throughout the mix and are not allowed to ‘clump’, creating fibre-free areas of concrete. The addition of specialist wetting agents will aid this process.
Once the concrete has cured, the effort required to de-bond, stretch and/or break the fibres within the matrix by tensile forces effectively reduce the incidence of surface cracking and the inherent brittleness of a concrete.
Small crack reduction
Synthetic fibresare beneficial in reducing the incidence of small cracks within the slab brought about by plastic shrinkageduring the curing process. They are often used in conjunction with steel fabric.
The main benefit of fibres, whether steel or plastic, is that they are uniformly distributed throughout the full depth of the concrete, which means the reinforcement is fully three dimensional.
Mesh or fibres are also used to control the width, spread and spacing of the cracks. Plastic shrinkage cracking occurs when the rate of water evaporating from the surface exceeds the rate of water rising to the surface from within the concrete, the latter known as bleeding.
Curing
If this rate of water loss is controlled by proper curing, such as the use of spray-on curing membranes, or covering with plastic sheeting, etc. much of the unavoidable cracking will be suitably controlled and managed.
Macro synthetic is becoming more popular for use in ground floor slabs, particularly for the smaller type of building such as commercial offices, schools, grain stores. They are about half the cost of steel fibres.
Final benefit
Together with improved crack control, the addition of fibres to a concrete mix has been shown to improve impact resistance and hardness, reduce segregation of aggregates and the incidence of bleeding during the curing process. It reduces permeability after curing and provides better frost and fire resistance in the finished slab.