The Geogrid Factory Revolution: How Modern Facilities Are Transforming Infrastructure
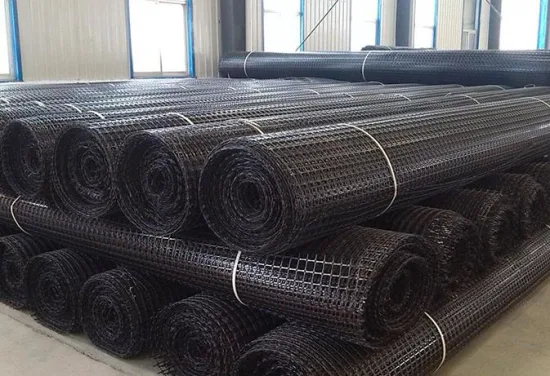
Geogrids have become indispensable in modern civil engineering and construction, providing essential reinforcement for soil stabilization, erosion control, and load distribution. As infrastructure projects grow in complexity and scale, the role of geogrid factories in delivering high-quality materials has become increasingly crucial. This blog explores how modern Geogrid factory are revolutionizing the industry, incorporating advanced technologies, and setting new standards for performance and sustainability.
The Evolution of Geogrid Manufacturing
1. Traditional Manufacturing Methods
Historically, geogrid production involved manual processes and limited technology. Early geogrids were simple in design and produced using basic extrusion and punching methods. These methods had limitations in terms of precision, consistency, and material performance.
2. The Advent of Modern Technologies
Modern geogrid factories have embraced cutting-edge technologies that have transformed the manufacturing landscape. Key advancements include:
- Automated Production Lines: Automation has streamlined the production process, increasing efficiency and consistency. Automated extrusion, stretching, and punching machines ensure high-quality geogrids with precise dimensions and grid patterns.
- Advanced Materials: New polymer formulations and additives have enhanced the performance of geogrids. Innovations such as high-strength polymers and eco-friendly materials have expanded the range of applications and improved durability.
Key Innovations in Modern Geogrid Factories
1. High-Tech Manufacturing Equipment
Modern geogrid factories are equipped with state-of-the-art machinery that enhances production capabilities. Notable equipment includes:
- Extrusion Machines: High-precision extrusion machines produce geogrid sheets with consistent thickness and quality.
- Stretching Equipment: Advanced stretching equipment ensures uniform orientation of the polymer chains, resulting in improved tensile strength and performance.
- Punching and Forming Tools: Sophisticated punching tools create intricate grid patterns with high accuracy, while forming machines ensure the final product meets design specifications.
2. Enhanced Quality Control Processes
Quality control is critical in geogrid manufacturing, and modern factories employ rigorous testing methods to ensure product reliability. Key quality control processes include:
- Material Testing: Testing for tensile strength, elongation, and permeability ensures that geogrids meet performance standards.
- Performance Testing: Geogrids undergo load distribution and reinforcement tests to confirm their effectiveness in real-world applications.
- Standards Compliance: Adherence to industry standards such as ASTM and ISO guarantees that geogrids meet international quality and safety requirements.
3. Sustainable Manufacturing Practices
Sustainability has become a central focus in modern geogrid manufacturing. Geogrid factories are adopting eco-friendly practices to reduce their environmental impact. Key initiatives include:
- Energy Efficiency: Factories are implementing energy-efficient technologies and processes to minimize energy consumption and greenhouse gas emissions.
- Recycling: Incorporating recycled materials into geogrid production helps reduce waste and supports circular economy practices.
- Sustainable Materials: Development of biodegradable and low-impact materials contributes to environmental sustainability.
4. Customization and Innovation
To meet diverse project requirements, geogrid factories offer customized solutions and innovative designs. Key areas of customization include:
- Custom Grid Patterns: Factories can design geogrids with specific grid patterns tailored to unique project needs, enhancing performance and functionality.
- Specialized Coatings: Applying specialized coatings can improve resistance to environmental factors such as UV radiation and chemical exposure.
- Innovative Solutions: Ongoing research and development lead to new geogrid designs and materials that address emerging challenges and applications.
The Impact of Modern Geogrid Factories on Infrastructure Projects
1. Improved Performance and Durability
Modern geogrid factories produce materials with enhanced strength, durability, and performance. This translates to:
- Increased Load-Bearing Capacity: High-strength geogrids provide superior reinforcement and load distribution, reducing the risk of soil failure and improving structural stability.
- Enhanced Soil Stabilization: Geogrids effectively stabilize soil in challenging conditions, preventing erosion and maintaining integrity in embankments and retaining walls.
2. Cost-Effectiveness and Efficiency
The advancements in geogrid manufacturing contribute to cost savings and efficiency in infrastructure projects. Benefits include:
- Reduced Construction Costs: High-performance geogrids reduce the need for additional reinforcement and maintenance, lowering overall construction costs.
- Faster Project Completion: Automated production and efficient manufacturing processes accelerate project timelines, enabling quicker completion of infrastructure projects.
3. Environmental Benefits
Sustainable practices in geogrid manufacturing support environmental goals and contribute to greener construction practices. Benefits include:
- Lower Environmental Impact: Energy-efficient production and the use of recycled materials help minimize the environmental footprint of geogrid manufacturing.
- Long-Term Sustainability: Durable geogrids contribute to the longevity of infrastructure projects, reducing the need for frequent repairs and replacements.
Case Studies: Geogrid Innovations in Action
1. Urban Infrastructure Projects
In urban development projects, modern geogrids have been used to enhance the stability of roadways, retaining walls, and green spaces. Innovative geogrid designs have improved load distribution and soil reinforcement, addressing challenges such as high traffic loads and limited space.
2. Environmental Restoration
Geogrids have played a crucial role in environmental restoration projects, including erosion control and land reclamation. Sustainable geogrid materials and advanced manufacturing techniques have facilitated successful restoration efforts, promoting soil stability and ecosystem health.
3. Large-Scale Construction Projects
In large-scale construction projects such as highways and bridges, modern geogrids have provided essential reinforcement and stability. High-strength geogrids have supported complex engineering solutions, ensuring the structural integrity and safety of critical infrastructure.
Conclusion
The geogrid factory revolution has transformed the industry with advancements in technology, sustainability, and customization. Modern geogrid factories are setting new standards for performance, efficiency, and environmental responsibility. By embracing these innovations, stakeholders can enhance the quality and success of infrastructure projects, contributing to more resilient and sustainable construction practices. As the industry continues to evolve, geogrid factories will play a vital role in shaping the future of civil engineering and environmental management.