Beyond the Blueprint: Innovative Applications of CNC Milling in Part Production
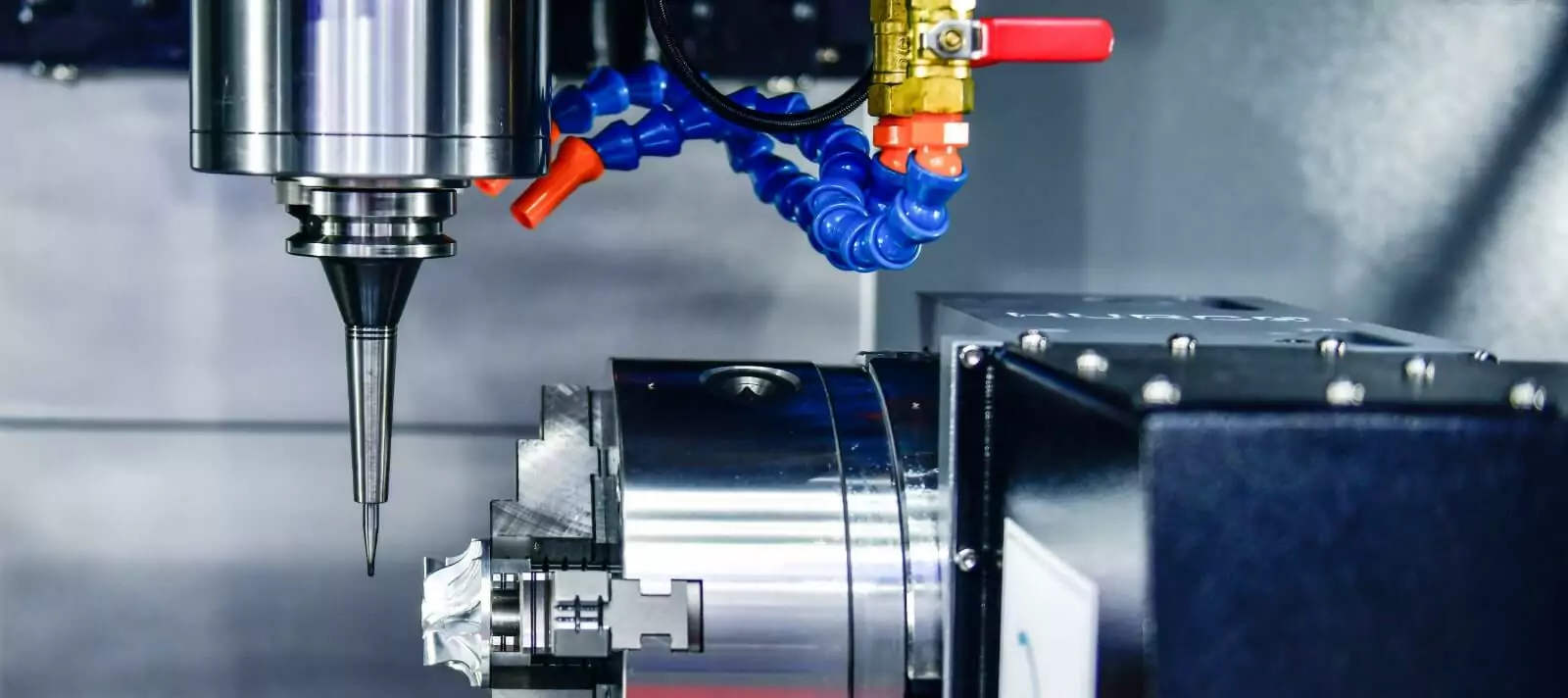
Computer Numerical Control (CNC) milling is no longer just a tool for making components from drawings in the industrial industry. CNC milling is leading the way in innovation these days, propelling improvements in part manufacturing in a variety of sectors. Beyond the limits of traditional production processes, cnc milling parts has found creative uses in a variety of industries, including consumer electronics, healthcare, and automotive. This piece delves into the cutting edge field of CNC milling, examining its creative uses and revolutionary effects on part manufacturing.
Unlocking creative flexibility:
By enabling engineers and designers to push the frontier of what is feasible, CNC milling offers unmatched creative flexibility. The limits of manual machining limit traditional manufacturing techniques, whereas CNC milling allows for the production of parts with exquisite features, complicated geometries, and organic forms. Because of this design freedom, part production may become more innovative and lead to the development of components that are stronger, lighter, and more efficient than in the past.
Rapid prototyping:
Using CNC milling as a catalyst to shorten the time it takes to build a product is one of the most inventive uses of the technology. Through rapid and accurate conversion of digital drawings into tangible prototypes, CNC milling helps designers to swiftly iterate and develop their ideas. By using an iterative approach to prototyping, design concepts may be tested and validated more thoroughly while also cutting down on development costs and time to market.
Personalization and Customization:
CNC milling makes it possible to mass customize products in order to meet the unique needs and preferences of each client. CNC milling may create items with distinctive features and specifications catered to the end-user, whether they are bespoke automobile components, customized consumer electronics, or medical implants. In addition to improving user experience, the ability to personalize and customize parts creates new possibilities for market segmentation and product differentiation.
Complex Machining Operations:
CNC milling excels at performing complex machining operations that are challenging or impossible to achieve with conventional machining methods. From multi-axis machining to simultaneous milling of multiple surfaces, CNC machines can execute intricate toolpaths with precision and efficiency. This capability is particularly valuable in industries such as aerospace and automotive, where parts often have complex geometries and tight tolerances.
High-Volume Production:
While small batch production and prototyping are frequently linked with CNC milling, it is also a good fit for high-volume manufacturing. CNC milling is now a very effective method for creating large quantities of components with consistent quality and dependability because to advancements in automation, tooling, and machining methods. Manufacturers may use CNC milling to accomplish high-volume manufacturing at a reasonable cost by utilizing economies of scale and streamlining production workflows.
Multi-Material Machining:
Metals, polymers, composites, and even sophisticated ceramics may now be machined using CNC technology. Because of the material’s adaptability, producers may create components with a wide range of features and attributes that are suited to certain application needs. High-strength titanium implants for medical devices or lightweight aluminum components for aerospace applications may be made precisely and accurately using cnc milling parts.
Additive Manufacturing Integration:
New opportunities for hybrid manufacturing processes have been created by the combination of CNC milling with additive manufacturing technologies, such as 3D printing. Manufacturers may take use of the design freedom offered by 3D printing together with the accuracy and smooth surface finish of CNC milling by merging the advantages of both additive and subtractive production processes. Complex components with improved performance characteristics and optimal geometries may be produced thanks to this hybrid technique.
Digital Twin Production:
Digital twins, or virtual copies of real assets used for analysis, optimization, and simulation, are largely produced by CNC milling. CNC milling guarantees that digital twins faithfully replicate real-world components by producing parts with high precision and fidelity, allowing engineers to confidently conduct virtual testing and analysis. Predictive maintenance, performance improvement, and design validation are made easier in a variety of sectors by this digital twin production method.
Sustainable Manufacturing Practices:
By cutting down on material waste, energy usage, and streamlining production processes, CNC milling helps to promote sustainable manufacturing practices. Advanced machining techniques, such adaptive tool path optimization and high-speed machining, enable manufacturers to minimize their environmental impact and maximize material usage rates. The sustainability of CNC milling operations is further improved by the capacity to recycle and reuse machined materials.
Industry 4.0 Integration:
CNC milling is becoming into a crucial component that makes smart production systems possible in the age of Industry 4.0. Through the integration of CNC machines with digital technologies like cloud computing, data analytics, and Internet of Things sensors, manufacturers may establish highly automated, flexible, and adaptable production environments that are networked. This connection opens the door for the factory of the future by enabling remote control, predictive maintenance, and real-time monitoring of CNC milling machines.
At the end:
In summary, the creative uses of CNC milling in part production are changing the face of contemporary industry. Numerous advantages of cnc milling parts, ranging from customization and sustainability to design flexibility and quick prototyping, spur efficiency and competitiveness in a variety of sectors. CNC milling will remain a key component in defining the future of manufacturing as new horizons of creativity, efficiency, and sustainability open up as technology develops and new opportunities arise.